Our Blog
Proudly Serving Canadian Industry
Since 1930
Blog
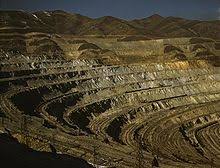
United States Copper Mine - Case Study
Eaton’s Airflex clutches are ready to support full-swing production when an Arizona copper mine is reopened at the end of 2012. Closed since 2009 due to the global economic downturn, the mine will produce copper concentrate to serve the global economy.
Eaton Airflex Ventilated Constricting (VC) clutches transmit the rotary torque from 4,000-horsepower low-speed synchronous motors, which operate six ball mills that grind the ore in preparation for copper extraction.
The Airflex clutches were supplied to the mine by Palmer Johnson Power Systems, an Eaton distributor in Phoenix, Arizona.
“Eaton’s Airflex engineering team designed and produced drop-in clutch replacements and delivered the complete retrofit packages in a very timely manner, which was of paramount importance to our operations.”
Mine Superintendent
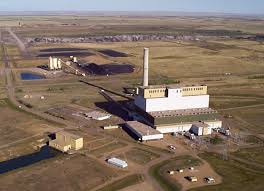
Sheerness Mine - Case Study
The Sheerness Generating Station, co-owned by TransAlta and ATCO Power, is located northeast of Calgary, Alberta, and is a major employer of residents in the local farming communities surrounding the station. The coal-fired power plant’s two generating units produce approximately 5.5 million megawatt-hours of energy annually.
The station relies on Sheerness Mine, a nearby coal mine. A key factor in providing coal for the station is the mine’s BE1300 electric dragline excavator, which runs 24 hours per day at a cost of thousands of dollars per hour.
The dragline bucket is operated using hoist and drag cables. Each cable system has a drum, driven through a gearbox by two motors, and each of the four motors uses traditional drum/clamshell braking systems.